What happened to all that PFAS-filled foam collected in New Hampshire?
Published: 01-03-2025 2:11 PM
Modified: 01-06-2025 4:01 PM |
They’re called “forever chemicals” but the program destroying PFAS in New Hampshire firefighting foam shows that a better name might be “everywhere chemicals.”
“They really are everywhere,” said Amy Dindal, business line director for Battelle, a national nonprofit which has a lab in Norwell, Mass., that looks for traces of PFAS in items ranging from industrial equipment, fire suppressants and medical devices to the livers of cows.
Cow livers?
“It can go from the water to the soil, from the soil to the grass, from the grass to the cows, from the cows to the milk,” said Franco Pala, lab director, during a recent tour of the facility.
The many chemicals known as per- and poly-fluoroalkyl substances, or PFAS, have become part of a huge number of manufacturing processes since they were developed in the 1940s because of the way they resist moisture and oils. They can be found in cookware, carpets, clothing and cosmetics, in the equipment that makes computer chips and in packaging that holds foods – almost anywhere, in fact.
The chemical structure of different types of PFAS, in particular the very strong carbon-fluorine bond, means they don’t break down in nature - hence the “forever” tag. As a result the chemicals have shown up in unwanted places, including water supplies, all around the globe from remote forests, to Arctic snows, even the bottom of the ocean.
That caused a real panic when the link between PFAS and the increased risk of various cancers was uncovered. Now there’s a race to find and deal with PFAS throughout the world, which is where Battelle comes in.
Battelle, which dates back to 1923, is a non-profit that funds research and development in a variety of fields. It developed a system that it calls the PFAS Annihilator and gave it to a spin-off called Revive Environmental, while Battelle itself concentrates on testing for PFAS.
Article continues after...
Yesterday's Most Read Articles
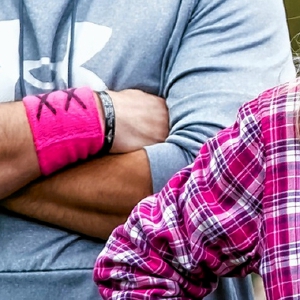
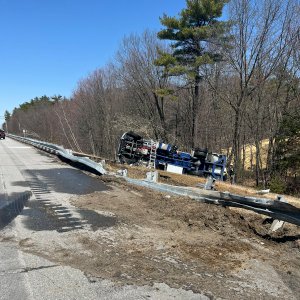
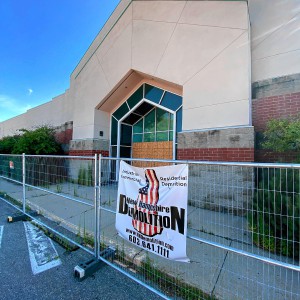
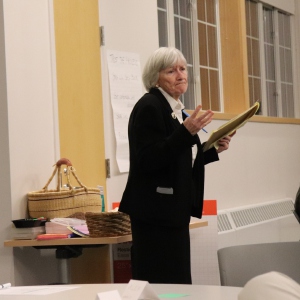
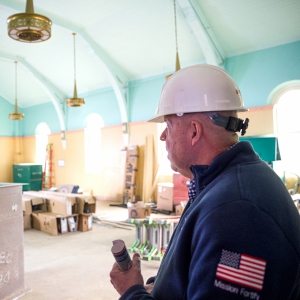
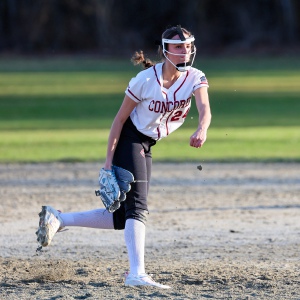
New Hampshire first faced the problem of PFAS contamination when the chemicals were found in groundwater near the Saint-Gobain plant in Merrimack in 2016. Concern has since spread to PFAS in many other sources with a focus on aqueous film-forming foam used for decades by firefighters. The foam contains a relatively high percentage of PFAS that can easily spread into the environment and may be linked to high levels of cancer in some fire departments.
In 2019, New Hampshire banned the use of the foam, known as AFFF or “A3F”, and created a program to collect it from hundreds of fire stations and military bases where it had been stored for years, sometimes decades.
Last summer, 10,000 gallons of collected AFFF was shipped from New Hampshire to Revive Environmental’s plant in Columbus, Ohio. The earliest foam dates from 1997.
There it is being run through the PFAS Annihilator. That room-sized machine uses a process known as supercritical water oxidation to break the carbon-fluoride bond and, Revive says, produce a residue with undetectable levels of the chemical.
There is no shortage of work for Revive, an independent company half-owned by Battelle that has just undergone Series A financing. Much of the initial work involves fire-fighting foam from fire departments, including huge stockpiles of the material at airports. Rick Gillespie, chief commercial officer of Revive, said that oil and gas refineries also have huge amounts of the material to be purified. “Landfill leachate, that’s another area, we’re helping customers process that,” he said.
The company has expanded to 32 employees and has a $5 million backlog of orders.
The cleaning process for the AFFF brought from New Hampshire starts with a 5-gallon bucket full of the stuff. The material is pumped into the room-sized Annihilator system, which isn’t as simple as it sounds.
“Some AFFF is thick as molasses, some is thin as water,” said David Trueba, CEO of Revive, during the video tour. Because the foam has been made for decades by multiple firms using different processes, “there is a very wide range of different formulations. We have almost 100 different types of AFFF from New Hampshire alone.”
Inside the Annihilator this goop undergoes chemical processes in high pressure (3,100 PSI) and temperature (600 degrees C) for between one and three minutes. This breaks the carbon-fluorine bonds and turns PFAS into carbon dioxide, a few salts, and water – a lot of water.
A video tour of the facility shows dozens of 275-gallon industrial totes stacked three high in the 11,000-square-foot factory, each holding water that had been run through the Annihilator and was waiting to be dumped.
That is where Battelle’s Massachusetts plant comes in. Revive needs its certification about the cleanliness of samples taken from each tote before they can dispose of the water.
Battelle’s plant was accredited in 2016 for detecting PFAS at the microscopic levels mandated for safety and has been expanding as the need becomes more and more obvious.
“There are 600 types of PFAS. Most labs look at 40 types. We can look at all of them,” said Dindal.
One complication is that the amount of PFAS linked to cancer is minuscule: The EPA’s drinking water standard for PFOS, one type of PFAS, is 4 parts per trillion, equivalent to a single drop in an Olympic swimming pool. This means that even a small amount of tainted outside material can ruin one of Battelle’s tests.
“Contamination is our biggest problem,” said Pala.
Before it can do any work, Battelle must ensure that PFAS won’t be released by anything in the rooms, including the lab coats worn by the 30 members of the laboratory staff and the containers which hold test material.
“We have to make sure that every component is PFAS-free before we even use them,” said Dindal. Usually that requires doing their own analysis because “sometimes the companies don’t even know if it’s there, they don’t know if their providers use it.”
In fact, a portion of the lab’s contracts now exist with companies that are unsure if their products meet new standards for the chemicals, which is why they test things like cat food and grain supplies.
There’s not likely to be any shortage of potential customers for Battelle or other testing facilities as more polluted sites and more sources of PFAS contamination come to light.
David Brooks can be reached at dbrooks@cmnitor.com